Deciphering the Complexities of Lift Technology: Troubleshooting Common Issues Throughout Lift Versions
From slow-moving operation problems to strange sounds originating from the machinery, repairing typical troubles throughout different lift versions requires a keen eye for detail and a methodical strategy. Keep tuned as we navigate with the labyrinth of lift breakdowns, seeking remedies to the enigmatic troubles that can interfere with the smooth functioning of these important apparatuses.
Recognizing Slow Operation Issues
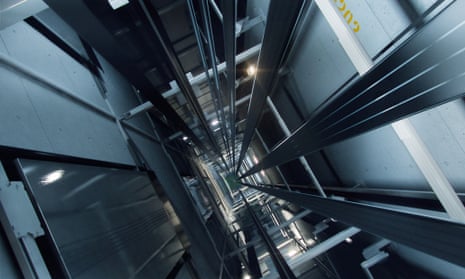
Next, check the electric links to guarantee that all components are correctly linked and operating. Malfunctioning electrical wiring or loosened connections can bring about reduce operation or full malfunction of the lift system. Additionally, it is vital to test the control system to establish if the issue hinges on the programming or sensors.
If the aesthetic evaluation and electrical checks do not reveal the source of the sluggish operation, more diagnostic tests might be essential. These can include stress examinations for hydraulic systems, voltage tests for electrical parts, or running diagnostic software program for the control system. repair and maintenance services. By following an organized method to troubleshooting sluggish operation concerns, you can effectively identify and fix the issue, making certain the lift operates securely and effectively
Addressing Strange Noises
To effectively troubleshoot lift technology for weird sounds, a thorough examination of the lift parts complying with the recognition of sluggish procedure problems is imperative. Odd sounds in lifts can be a sign of underlying issues that call for prompt attention to make certain the safety and security and reliability of the system. Common resources of odd noises in lifts consist of worn-out or misaligned wheels, damaged electric motor bearings, broken or loose suspension ropes, and malfunctioning control systems. When resolving strange noises, it is important to carry out a methodical assessment of these parts to pinpoint the exact source of the noise accurately. This may entail looking for any kind of noticeable signs of damage, examining the functionality of electric motor bearings, tightening up loosened connections, and lubing moving components as needed.
Furthermore, it is vital to refer to the lift supplier's upkeep guidelines and look for assistance from qualified service technicians when handling intricate lift parts or unknown troubleshooting treatments. By immediately dealing with and resolving unusual sounds underlying problems, lift operators can guarantee the optimum performance and safety and security of the lift system for guests and drivers.
Resolving Faulty Control Issues
An efficient strategy for dealing with defective control troubles in lift innovation involves carrying out an extensive assessment of the control system's elements and performance. When running into problems with lift controls, it is crucial to very first look for any kind of loosened links, damaged electrical wiring, or malfunctioning sensing units. Validating that all control keypads, switches, and display screens are operating properly is also important in detecting the problem accurately.
If no visible issues are evident, specialists must continue to check the control board for any type of indicators of water overheating, deterioration, or damages, as these can commonly lead to regulate malfunctions. In addition, resetting the control system or updating the software application might help fix specific problems or pests creating the issue.
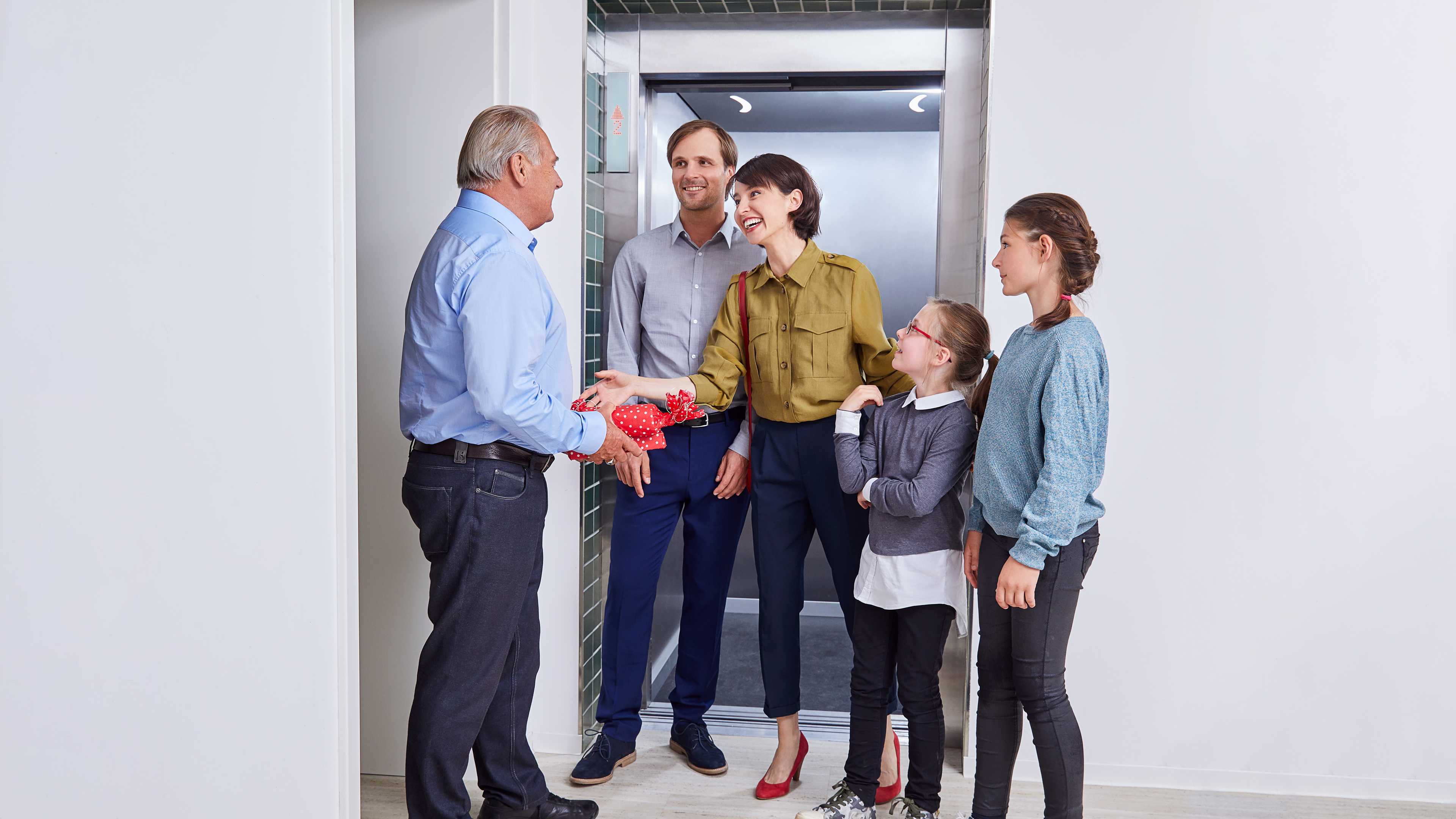
Tackling Hydraulic System Malfunctions
The efficiency of hydraulic systems in lifts counts greatly on the proper performance of different parts within the system. When hydraulic systems malfunction in lifts, it can lead to operational disruptions and security concerns.
One more regular hydraulic system breakdown is a loss of pressure, which can arise from air entering the system, fluid contamination, or pump ineffectiveness. Service technicians can address this by hemorrhaging the system to remove air, replacing contaminated fluid, or servicing the pump as required. Furthermore, abnormalities in hydraulic fluid look at this web-site levels or uncommon noises during lift operation might indicate underlying system malfunctions that need instant focus to avoid further damage. Normal upkeep and prompt troubleshooting of hydraulic system concerns are critical to making certain the reliable and safe operation of lift modern technology.
Dealing With Electric Component Failings
Addressing electrical part failures in lift technology demands an organized strategy to identifying and fixing concerns to preserve operational functionality and safety and security criteria. When running into electrical issues in lift systems, it is critical to very first carry out a comprehensive examination of the electric elements, consisting of control board, circuitry, sensing units, and circuit boards. Any indicators of damages, corrosion, loosened links, or scorched components should be meticulously kept in mind and addressed promptly to avoid more complications.
When it comes to electric part failures, it is necessary to adhere to supplier guidelines for repairing and repair procedures. This may include evaluating the elements making use of multimeters, oscilloscopes, or other diagnostic devices to identify the specific source of the malfunction. In addition, having a thorough understanding of the lift's electrical schematics and circuitry layouts can assist in recognizing and remedying problems successfully.
Routine maintenance and evaluation timetables can help avoid electrical failures by detecting potential issues at an early stage. Appropriate training for lift professionals on electrical systems and elements is additionally essential to ensure exact diagnosis and efficient resolution of electrical problems, inevitably adding to the general safety and reliability of lift operations.
Conclusion
Finally, fixing lift modern technology calls for a methodical method to recognize and address usual issues such as sluggish operation, weird noises, malfunctioning controls, hydraulic system malfunctions, and electric component failings. By understanding the intricacies of lift technology and following appropriate repairing actions, technicians can effectively resolve problems and make certain Visit This Link the risk-free and reliable procedure of lifts throughout numerous designs.
To properly troubleshoot lift innovation for helpful hints unusual noises, an extensive exam of the lift elements complying with the identification of slow-moving operation issues is necessary. Weird noises in lifts can be a sign of underlying issues that require timely focus to guarantee the security and dependability of the system.An efficient method for addressing faulty control issues in lift innovation entails carrying out a comprehensive assessment of the control system's elements and capability.The performance of hydraulic systems in lifts counts heavily on the correct functioning of different parts within the system. repair and maintenance services. When coming across electric problems in lift systems, it is important to first carry out an extensive evaluation of the electric components, including control panels, wiring, sensors, and circuit boards